
FM Logistic in context
FM Logistics, one of the leading international logistics players, offers a complete supply chain management service (warehousing and handling, transport & distribution, , co-packing and co-manufacturing). Independent and family-owned for more than 50 years, the group is recognized as an expert in consumer goods, retail, industry, beauty/cosmetics and health markets.
26,200 employees control 3.9 million sq. m. (41 million sq. ft.) of warehouse space and a fleet of 3,500 vehicles, FM Logistics turned 1.178 billion euros in revenues for 2017.
Par sa qualité d’écoute et la puissance de calcul du moteur d’ordonnancement, Planilog a parfaitement complété cette équipe projet, contribuant ainsi à l’amélioration de nos performances.
WAREHOUSE MANAGEMENT
FM Logistic has warehouses ranging in size from between 80,000m² (860,000 sq. ft.) and 130,000m² (1.4 million sq. ft.) and using different WMS (Warehouse Management System) solutions.
The transit time of goods on the loading docks is therefore a major challenge to increase productivity and reduce delays. To meet this challenge, FM Logistic has relied on a Lean & Continuous Improvement approach to define and build a solution based on the experience and field practices of its employees.
PLANILOG ALGORITHM
In collaboration with the FM Logistic teams, Planilog tailored its standard version application into an advanced scheduling solution based on a barycenter calculation (one based on the center of gravity between several points) in order to define the optimal loading platform and simplify the dock allocation process. This solution works on an algorithms engine aimed at optimizing distances covered by drivers combined with a real-time vision of dock occupancy (receiving and shipping).
The data assembly gives the Team Manager the ability to fully control his loading docks and advise each driver of fastest routes. Equipment rotation is therefore smoother, and waiting time reduced.The Team Manager also has daily access to statistics allowing him to see gaps between optimal recommendations and reality on the ground. It is a key part of Continuous Improvement process to establish and implement specific actions to reduce those shortfalls. Planilog’s planning and scheduling solution is therefore integrating data from the WMS tools already in place within the group. It fully integrates within the Corporate Information System and contributes to increased productivity. For example, order management process and time spent on administrative tasks decreased by 5 to 10%.
Ready to get started?
Start your free trial today or contact us if you have any questions.
Stay up to date with the latest information
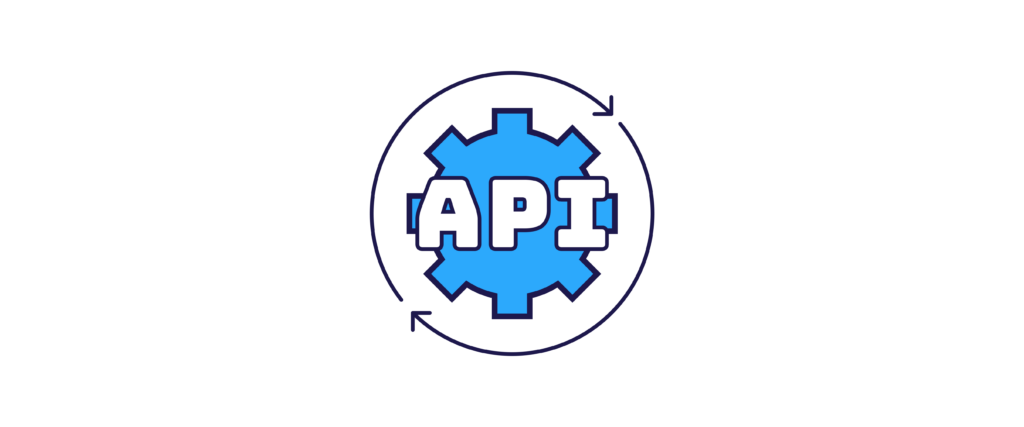
Simplifiez la gestion de vos données avec les API PLANILOG
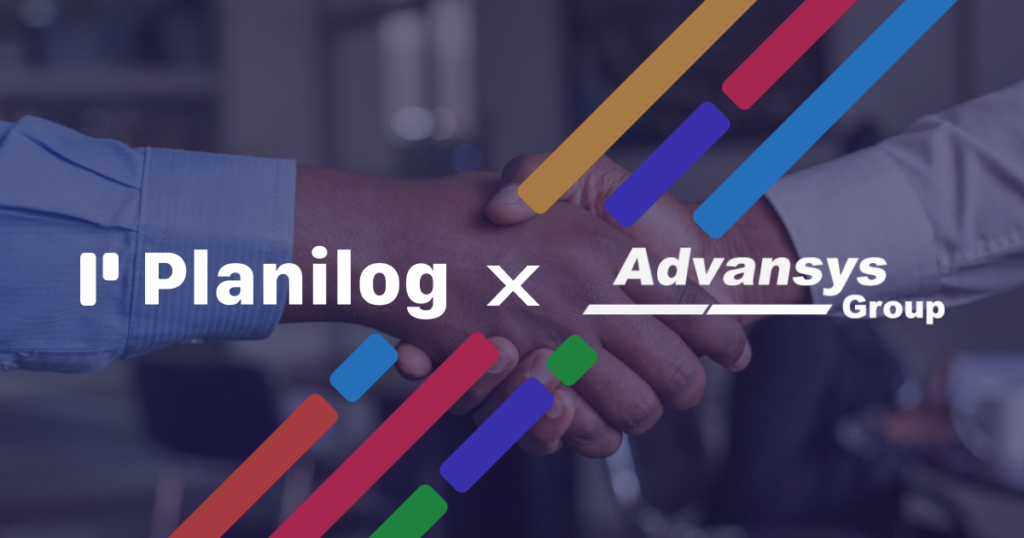
Nouveau partenaire : ADVANSYS Group, spécialiste manufacturing distribuera Planilog au Maroc !
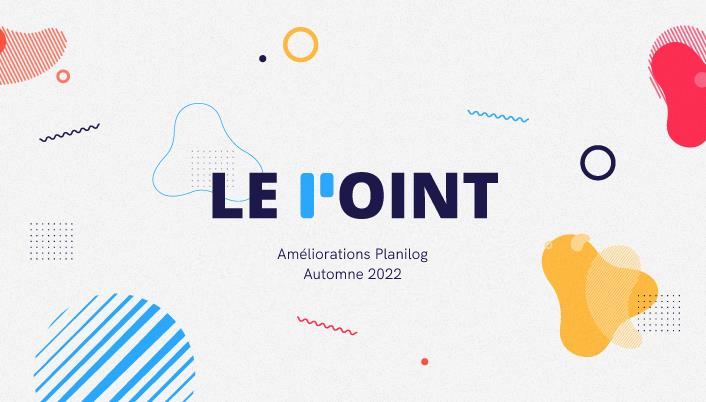
Les améliorations fonctionnelles de Planilog - automne 2022
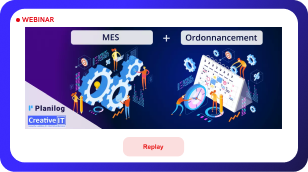
Une solution packagée MES + Ordo
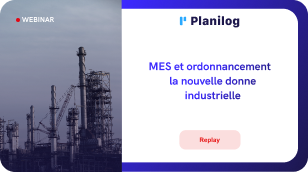
MES + Ordonnancement : la nouvelle donne pour gérer, planifier, suivre et mesurer efficacement !
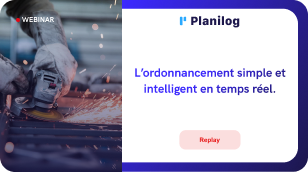
L’ordonnancement simple et intelligent en temps réel
Témoignage Nicolas Renard - La Manufacture Urbaine (S.E.M.U.)
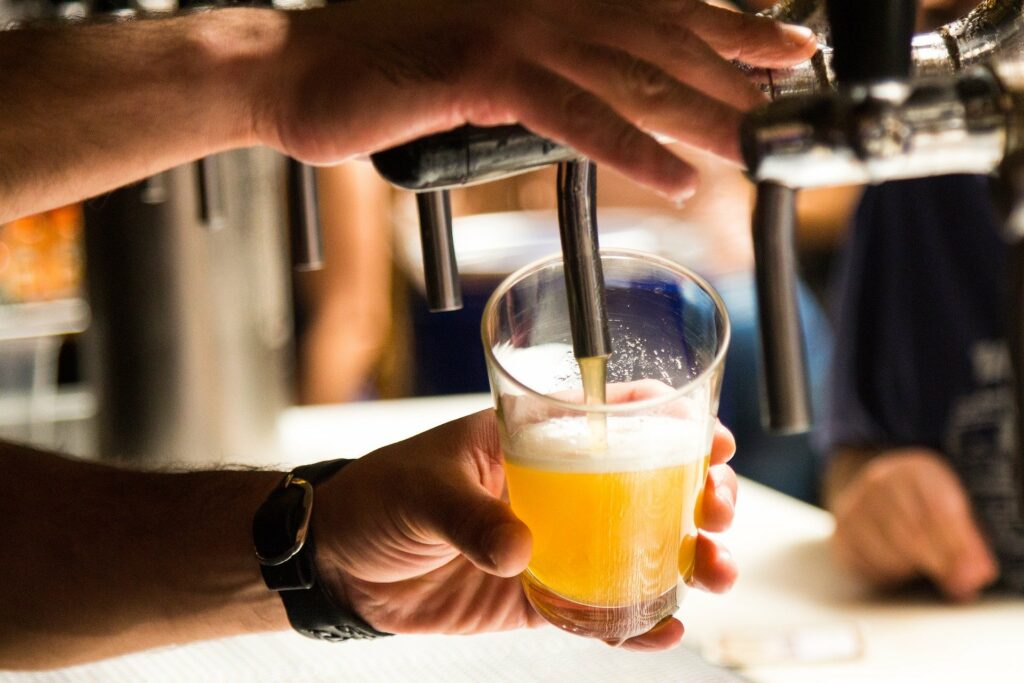
La Manufacture Urbaine (S.E.M.U.)
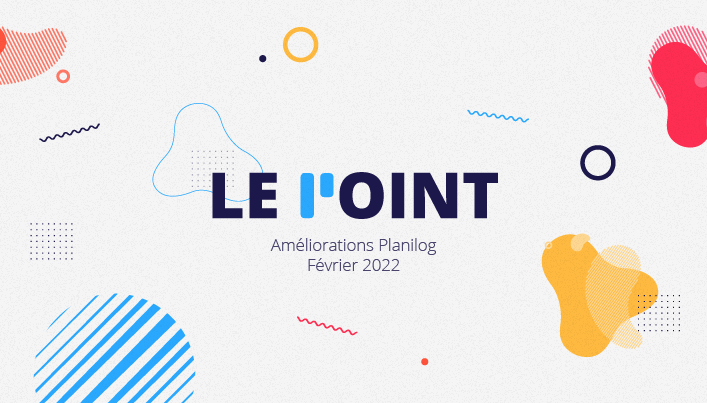
Les améliorations fonctionnelles de Planilog en cette rentrée 2022
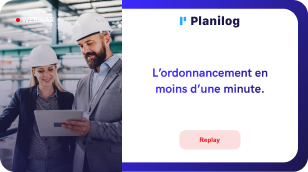
Ordonnancer de façon optimale en moins d'une minute, c'est maintenant possible !
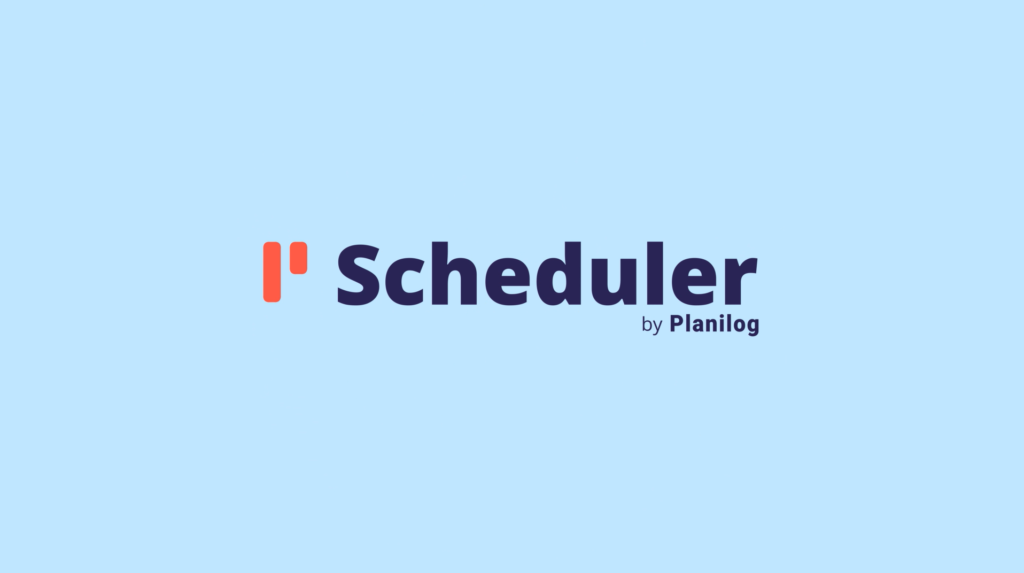
Planilog révolutionne l'ordonnancement avec le Scheduler
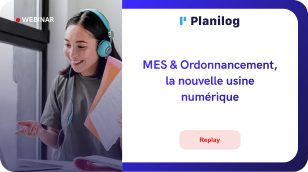